25%: this is the percentage of floor space used for effective storage (racks or other storage types) in an average warehouse. You were expecting more, right? In this post, we dive deeper into optimizing (floor space) utilization in your available space. Some may think this means cramming the warehouse with racks, worktables, transport equipment, etc. But nothing could be further from the truth. Together, we’ll explore what to consider when designing your warehouse layout to achieve an optimal and efficient result!
Preliminary Study
The first phase of setting up your warehouse, whether redesigning an existing space or starting from scratch, is conducting a preliminary study. Without a thorough analysis, you will never achieve a good result. However, this doesn’t have to be a complex study—just take the time to list all the relevant factors.
Gaining Experience
Setting up an efficient warehouse from scratch without any logistics experience is very difficult, if not practically impossible. If you lack experience, visit nearby companies you know or those that operate similarly. Observing other warehouses can provide valuable insights—both in what to adopt and what to avoid. With some luck, you might also receive useful tips and tricks about how they approached their setup and what they would or wouldn’t do again.
If you have prior experience in a logistics environment, write down what worked well and what didn’t in that particular setting, even if it was in a completely different industry. These insights will help you avoid repeating past mistakes and improve your layout from the start.
Defining Flows
A crucial step in effective warehouse design is thinking about the necessary flows in your environment, such as:
- Incoming goods
- Temporary holding area
- Incoming goods
- Outgoing goods
- Storage
- Order picking
- Packing
- Internal transport
- Waste disposal
- Office space
- Sanitary facilities
Always plan based on “worst-case” scenarios so you can anticipate potential issues. The layout will vary depending on the type of products you store and the number of people working in your warehouse. Analyze each step of your logistics process and determine the space and layout needed.
Don’t limit your planning to essential elements like storage and packing—also consider auxiliary activities such as waste management and safety equipment, which take up space. You’ll likely need an office area for administrative tasks as well.
Storage Techniques
A warehouse’s core function is storing goods. As mentioned earlier, an average of only 25% of the floor space is used for actual storage. The rest is allocated to aisles, waiting areas, packing tables, waste management, etc.
Depending on the types of products you store, different storage methods will be used. Some commonly used storage types include:
- Pallet racking
- Cantilever racking
- Shelving systems
- Picking bins
- Automated storage (e.g., AutoStore)
- Vertical storage (e.g., Kardex)
Equipment
Available warehouse equipment ensures a smooth transition between different flows. Key questions to consider:
- How will products move from point A to point B?
- How will orders be picked?
- Where and how will picked orders be packed?
- What happens to prepared orders?
All these tools require space (both during and after use), so include them in your warehouse layout:
- Pallet trucks (manual or electric—charging stations needed?)
- Forklifts or stackers
- Conveyor belts
- Picking carts
- Picking robots (goods-to-person, shelf-to-person, etc.)
- Packing tables
- Safety elements (fire extinguishers, first aid kits, etc.)
- Charging stations
- Computers and printers
Breathing Space
It may sound strange, but breathing space is a top priority in warehouse design. Without the necessary open areas, an efficient workflow will never develop. Adequate free space ensures visibility and calmness in the warehouse—two essential factors in daily operations. A cluttered environment can stress employees before they even start working, let alone having to navigate through it. While open space might seem costly, it ultimately saves money in many ways.
Smart Warehouse Layout
After your preliminary study—which could take hours, days, or even weeks—it’s time for the real work: translating theory into practice. But how do you do that?
Sketching the Layout
Start with a floor plan of your warehouse, showing only the walls, leaving everything else blank. This will serve as the foundation for outlining your layout. You can use a free program like SketchUp or go old-school with pen and paper (preferably printed on A3 size for better usability).

Defining Zones
Try to divide your main warehouse flows into different zones. Mark these zones roughly on the floor plan, ensuring a logical layout:
- Place the inbound zone where goods physically enter the warehouse.
- Position storage areas where different storage types will be located.
At this stage, don’t worry about details like aisle widths—it’s just about rough outlines.
Product Types and Turnover Speed
Storage areas can be further subdivided based on product type (large, small, food, organic, FIFO, FEFO, etc.) and turnover speed (A, B, or C items).
- About 20% of products will be A (5%) and B (15%) items—high-turnover products that should be stored close to the packing area.
- The remaining 80% are C items, which can be placed further back in the warehouse.
Minimizing the distance employees travel daily saves a significant amount of time and reduces physical strain over the long term.
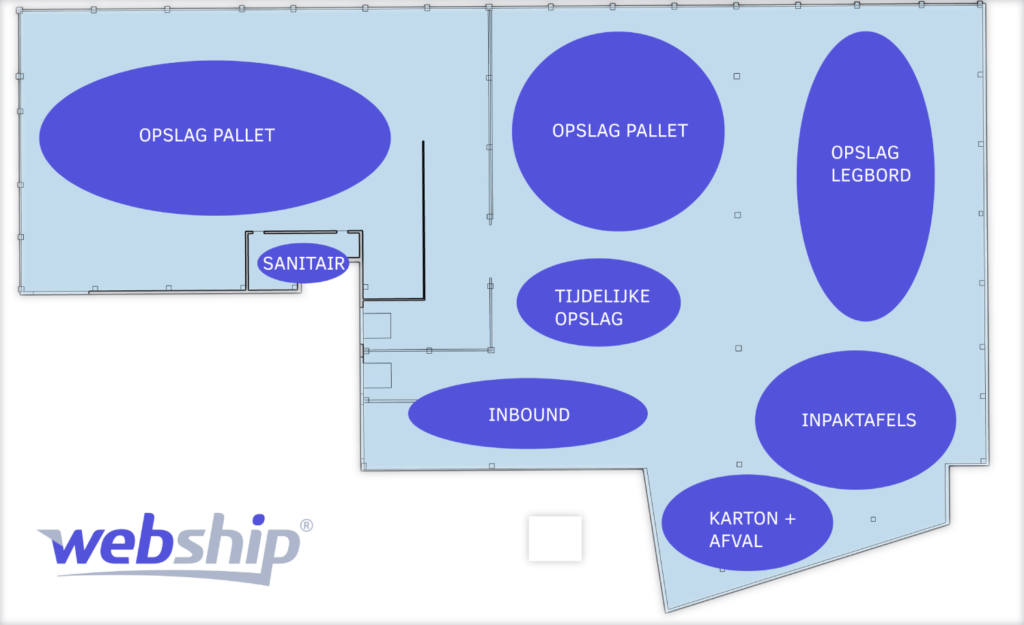
Dynamic Locations
Instead of fixed storage locations, use a dynamic system. Based on product characteristics, you can assign stock to specific areas. When a location becomes available, it can be used for similar products (e.g., A-items), but not necessarily the same exact products. This approach maximizes storage efficiency and reduces errors. However, a logical numbering system for locations is essential.
Detailed Planning
Once you’ve finalized the zoning on your floor plan, refine it further until you have a centimeter-accurate placement for everything—from the largest pallet rack to the smallest trash can.


We can’t emphasize this enough: allow for ample space. It’s better to have extra room than to struggle with a cramped layout later.
Avoid “smart” tricks like reducing aisle widths to fit more racks. Check equipment specifications (e.g., forklift dimensions) to ensure minimum recommended aisle widths. Design aisles so employees don’t have to wait for each other to pass.
With everything mapped out in detail, you can also decide on a logical numbering system and zone labeling. Will you use a house-number system (odd numbers on the left, even on the right), a “snake” system (numbering resets at the end of an aisle), or another method?
A good warehouse management system (WMS) can optimize picking routes based on your zones and numbering. This is crucial to avoid congestion and streamline inbound/outbound processes.
Physical Execution
After meticulous planning, it’s finally time for execution—the easiest step. While the planning process involved trial and error (revisions, adjustments, and refining), at this stage, there’s little room for major changes. Once suppliers are locked in, it’s just a matter of waiting and executing the plan.
Implementation
During implementation, minor adjustments can still be made—for example, shifting racks slightly left or right. However, try to stick to the plan unless there’s a compelling reason to change it.
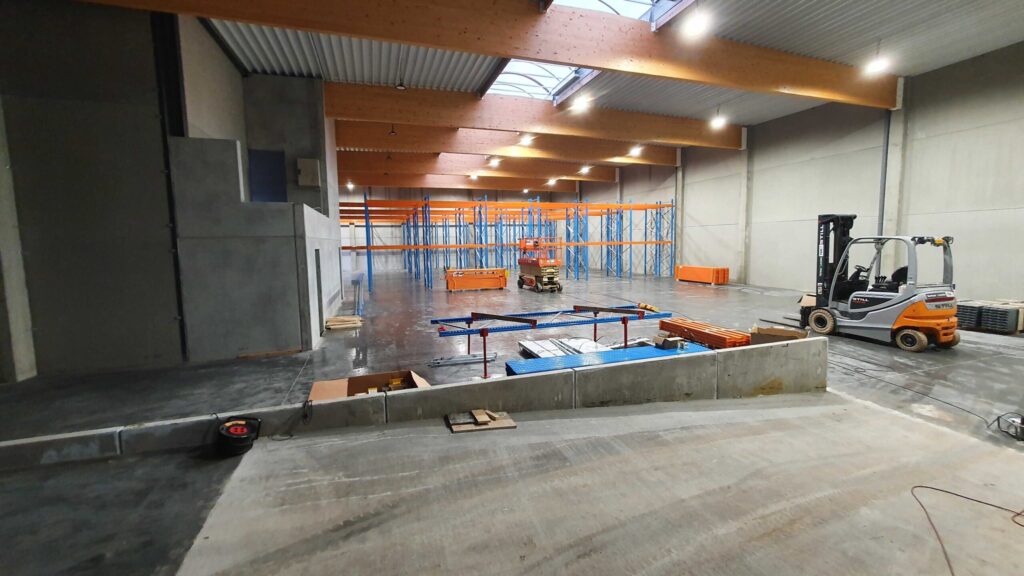
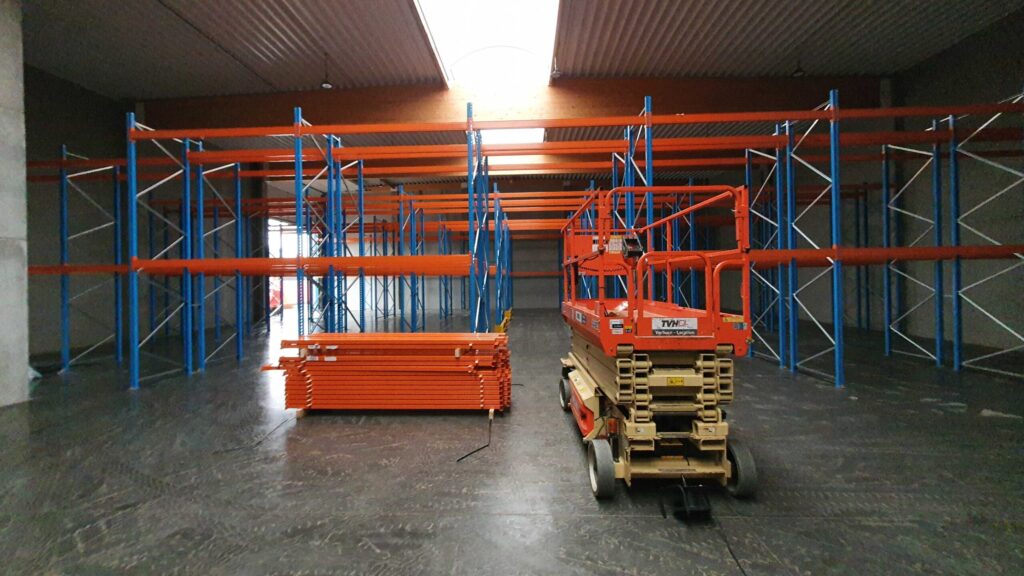
Go-Live
Once the warehouse is set up, it’s time to go live. You may want to integrate your physical layout into a Warehouse Management System (WMS) to digitally manage zones, location numbering, and stock registration.
Over time, adjustments will be necessary. That’s why it’s wise to leave some flexibility in critical areas to accommodate future changes.
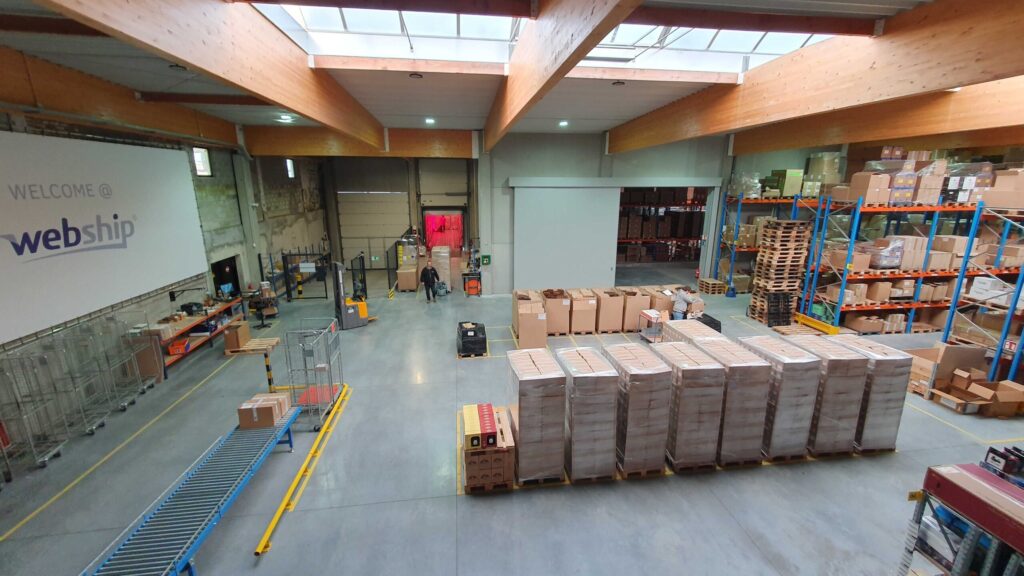
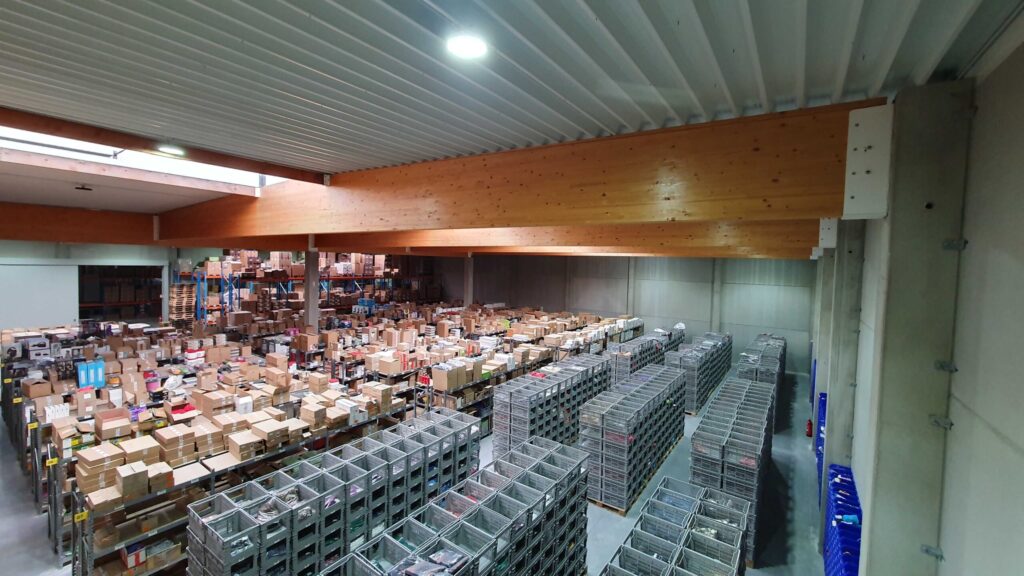
Conclusion
Designing an efficient warehouse layout is complex. While we covered key aspects, there’s much more to consider, such as internal transport (e.g., conveyor belts) or packing station setup.
Key takeaways:
- Plan your logistics flows thoroughly
- Start with a rough sketch and refine step by step
- Allow for sufficient breathing space
- Use reliable warehouse management software
- Adjust as needed